化学物質の自律的管理:実際どうやる??
やることリスト:
- 化学物質リストの作成(ケミカルインベントリー)
- リスクアセスメント
- ハザードコミュニケーション・教育
- 化学物質の導入精度・調達戦略
- 緊急事態対応
- 廃棄物のマネージメント
- 化学物質の保管
- 保護具
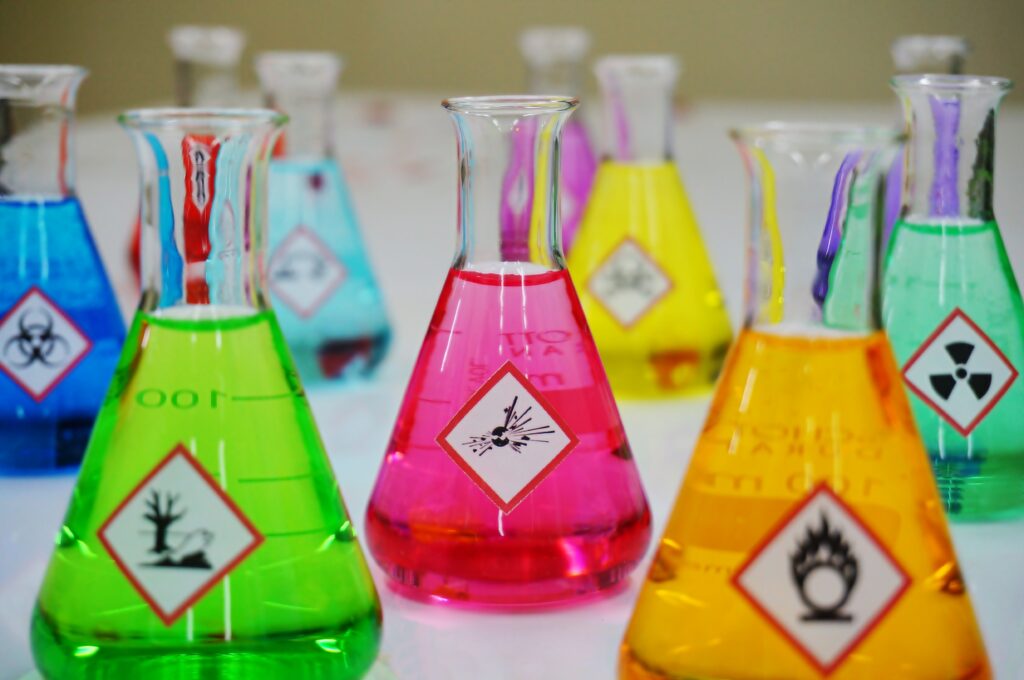
化学物質リストの作成(ケミカルインベントリー)
今回の法改正で、何から始めていいか分からない人は、まずここから始めましょう。 事業所で取り扱っている化学物質リストの作成です。 実はもう持っているという企業も多いかと思います。 しかし、今一度見直して、今回の法改正への対応やリスクアセスメントに必要な事項がそろっているか確認してみてください。
揃えておきたい情報としては以下となります:
- 最新版のSDS
- 使用場所
- 使用方法
- 使用量
- 使用時間
- 保管量
- 使用時の温度
- 使用時の保護具
- 現在取扱者が感じていること など
これらの情報を、事業所内にある全ての物質で取りそろえるのには、かなりの労力となります。 しかし、化学物質管理の基本は「知らないところで知らない化学物質を知らないまま取り扱わないこと」です。 多くの化学物質事故は「知らなかった」ことが原因となっています。 まず、ここを把握することで、「知らなかった」を避けましょう。
最新版のSDS:当たり前のように感じるかもしれませんが、これ実はかなり難しいものです。 例えば今回SDSを取りそろえると、それは最新版のSDSですから、その時点で完成となります。 しかし、3年後5年後10年後と考えるとどうでしょうか。 SDSに記載される内容も変わるかもしれませんので、最新版をキープしておく必要があります。 その場合、都度行うのか、数年ごとに全更新するのか、何年毎にするのか、その際のマンパワーはどうするのか、意外と決めることやることは多くなってきます。 どのような手法にするかは、規模やSDS総数によって変わってきますが、いざSDSが必要になった際に開いてみたら20年前の古いSDSだった・・・となることは避けるようにしましょう。
使用場所:たとえ同じ物質で同じ使用方法であっても、その使用場所によって大きくリスクが変わる場合があります。 例えば、換気のいい屋外、換気のいい屋内、ドラフト内、換気の悪い屋内、容器内、など、どんな場所で使用しているのか確認しましょう。
使用方法:これもリスクアセスメントに大きく関与します。 例えば塗装剤をスプレー塗装するのか、刷毛塗装するのか、使用物質や使用場所が同じであっても、そのリスクは大きく変わってきます。 揮発が大きくなるような使用方法については、使用方法(手順)を少し変えるだけでもリスクが軽減されるかもしれません。
使用量と使用時間:これらも明白ですね。 使用量や使用時間によって、そのリスクは大きく変動します。
保管量:これは無くてもさほど問題ではありませんが、あると便利です。 ここまで頑張って調べたのであれば、さらにひと手間あってもいいかもしれません。 物質によっては、保管自体にリスクがある場合があります。 例えば不安定な物質や、相いれない物質が一緒に保管されてしまう場合、地震があった際に破損・漏洩のリスクがある場合など、そこに化学物質が保管されているだけでリスクがある、ということも考えておきましょう。 在庫確認はどこでも実施していると思いますので、そこに上手く結びつくように管理ができると簡単かもしれません。
使用時の温度:これも明白ですね。 常温で使用するのか、熱して使用するのか、使用時の温度によって、揮発性が大きく変わります。 リスクアセスメントの結果にも大きく影響します。 この情報も入手するようにしましょう。
使用時の保護具:もちろん、リスクアセスメントの結果に応じて保護具を決定していくのですが、これからリスクアセスメントを導入しようとしている場合、多くの化学物質がすでに使用中の場合があります。 その場合、現在使用している保護具を確認しましょう。 現在使用している保護具を確認したところ、明らかに不足していると分かる場合は、その場で是正しましょう。 その他については、その後リスクアセスメントを実施し、保護具が十分な防護となっているのか確認していくこととなります。 リスクアセスメントの手法、保護具の決め方については後述します。
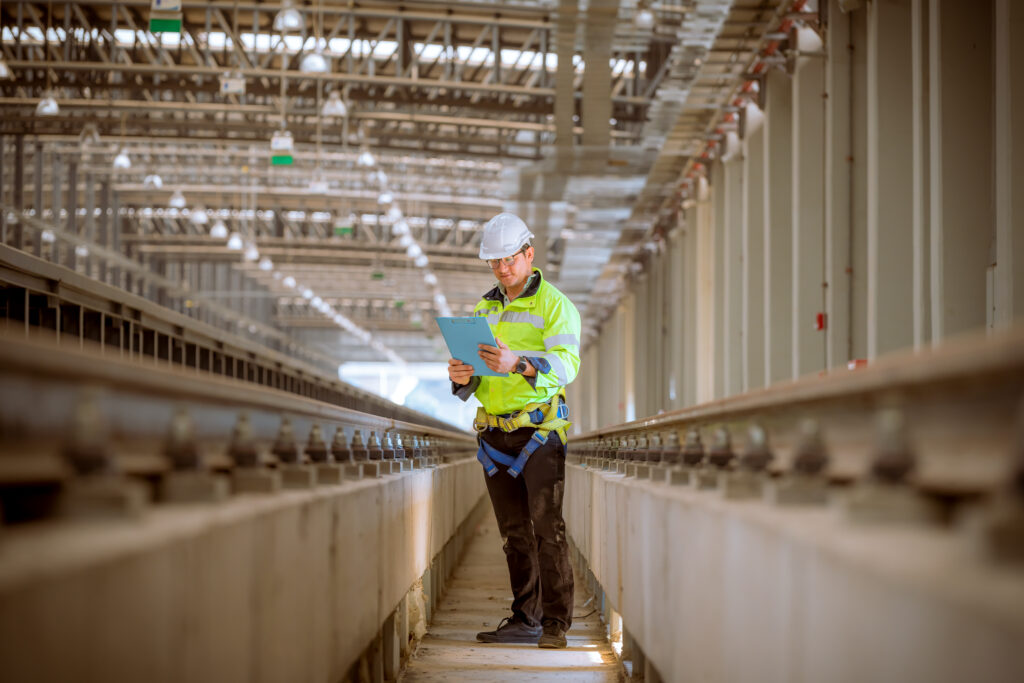
ウォークスルー調査
一般的な用語か分かりませんが、まずは「ウォークスルー調査」というものをおこないます。これは、実際にリスクアセスメントを実施する職場に歩いて回り、そのエリアにあるハザードやリスクといったものをリストしていくものとなります。先述したインベントリー作成と一緒にやってもいいですね。また、可能であればその職場で働く人々に話しかけてみるのも有益な情報となります。多くの場合、実はそこで働いている人は「ここが危ない」というのを分かっていたりします。それを聞き出せれば、そのエリアの優先度高いリスクを簡単に抽出することができます。もちろん分かっていない場合もあるので、そういった場合は作業を注意深く観察したり、聞き取りも工夫しなくてはなりません。聞き取り衣をするうえで一番気を付けなくてはいけないのは、口調です。決して「取り調べ」になってはいけません。あくまでフランクにフレンドリーに。にこやかな顔で話すことを心がけましょう。
このウォークスルー調査を実施し、どのようなハザードが職場にあるのか把握することが第一歩となります。小さな職場であれば一度回ればいいかもしれませんが、大きな職場では繰り返しウォークスルー調査を重ねることにより、精度の高いハザードリストの作成ができます。その後一つ一つにリスクアセスメントを実施し、測定の優先度を決めていくことになります。
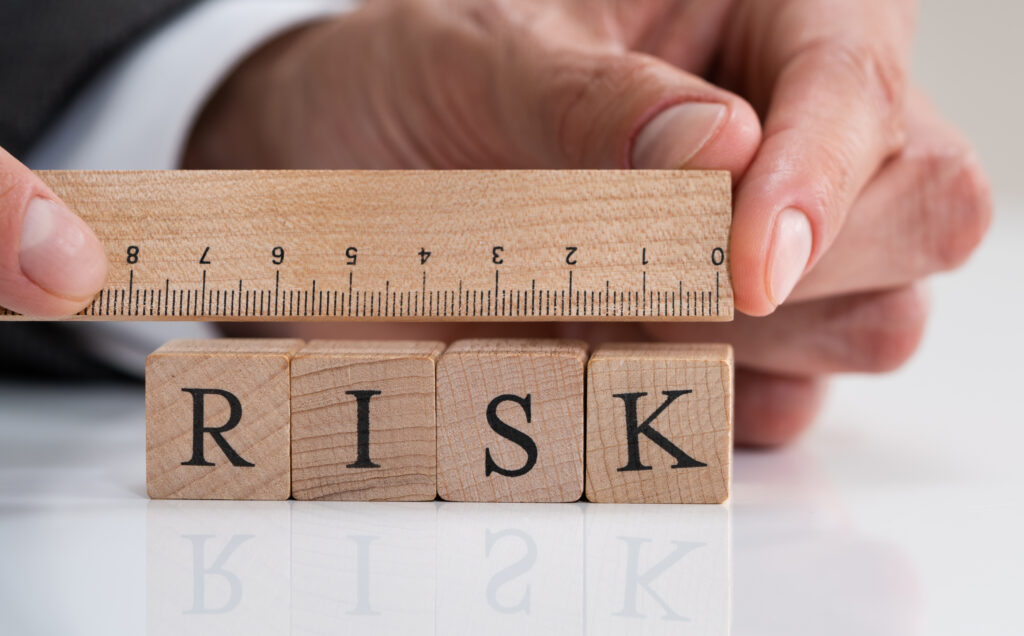
リスクアセスメント
さて、今回の目玉と言ってもいい「リスクアセスメント」です。 化学物質に係るリスクアセスメントと言っても、いくつかのリスクアセスメントがあります。 まずそれをフロー図で示してみます。
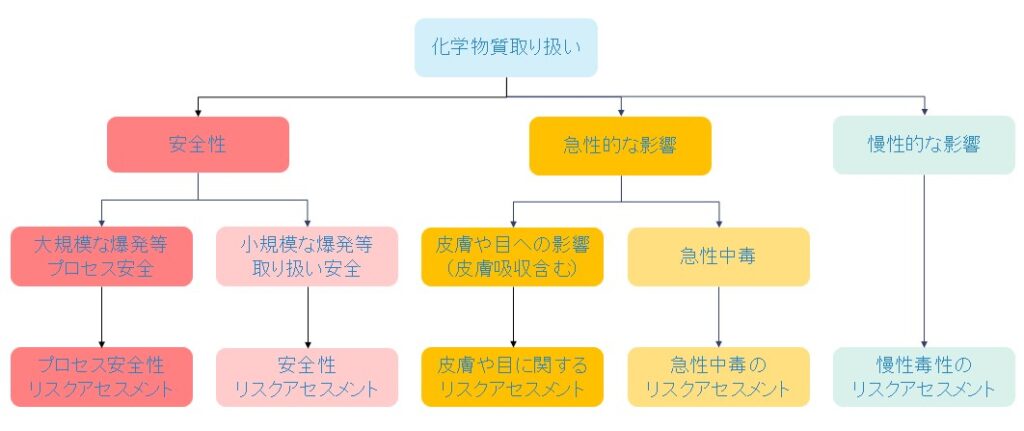
さて、いかがでしょうか。 思っていたより多い、というのが印象ではないでしょうか。 一つ一つのリスクは別のものであり、リスクアセスメントを混同してはいけません。 左側から一つづつ、簡単に紹介していきます
まず、プロセス安全性リスクアセスメントですが、これは装置の圧力バランス、温度、反応性、など、様々な部分を装置の図面上で確認していくリスクアセスメントとなります。 これは全く別の分野であり、Chemical Process Safety (CPS)と呼ばれています。 技術者としてはCCPS Process Safety Professional Certification (CCPSPC)などが有名です。 CPSと呼ばれているかは別として、化学物質製造プラントでは、こういった技術者がすでにいるのではないでしょうか。
続いて、安全性リスクアセスメントになります。 と言っても、リスクアセスメントというほどのことではありません。 化学物質は気化して引火する、爆発する、というのは当たり前のことですから、充満させないことが必須となってきます。 リスクアセスメントとしては、充満の可能性があるか、換気はどの程度あるか、強制換気は必要か、というのを事前に確認する程度かと思います。
皮膚や目に関するリスクアセスメント、これも法令に関係する大事なリスクアセスメントですね。 目の部分については、被液の可能性があるか、被液した場合の影響度はどのくらいか。
MORE COMING SOON
リスクアセスメントの手法も様々ありますので、ここでもいくつか代表的なものを紹介していきます。 もちろん、これが全てではありませんので、ここに記載されていないリスクアセスメントを実施しても問題ありません。 リスクアセスメントは大きく分けて二つ:定性的なリスクアセスメントと定量的なリスクアセスメントに分けられます。
- 定性的リスクアセスメント
- コントロールバンディング
- 改良型コントロールバンディング
- Create Simple
- マトリクスを用いたリスクアセスメント
- 数理モデル
- 専門家の「感覚」
- 定量的リスクアセスメント
- 個人ばく露測定
- 場の測定
- リアルタイムモニターを使用した測定
- 検知管を使用した測定
さて、定性的リスクアセスメントについては、結論を先に言うと、「専門家の感覚」でおこなうのが一番効率がよく、最善の手段だと思います。ただし、みなが専門家にアクセスがあるわけではないので、この話は最後に回します。
リスクアセスメントと言えばCreate Simpleですね。現在、厚生労働省をはじめ、様々な場所でこのCreate Simpleが紹介されています。誰でも簡単にリスクアセスメントを実施できるというのがメリットとなります。いろいろなところこで使用方法がすでに紹介されていますので、ここでの記載はやめておきます。
Create Simpleの使用方法やダウンロードはこちらから。
わたしがCreate Simple以外で使い勝手がいいかなと感じたのが、マトリクスを用いたリスクアセスメントです。これは、有害性とばく露の程度を調べ、マトリクスを用いてリスクを導き出すものとなります。使い方が分からないと少し難しいのですが、これは練習あるのみですね。これは厚生労働省が出したマトリクス法ですが、正直あまりポピュラーではないようです。
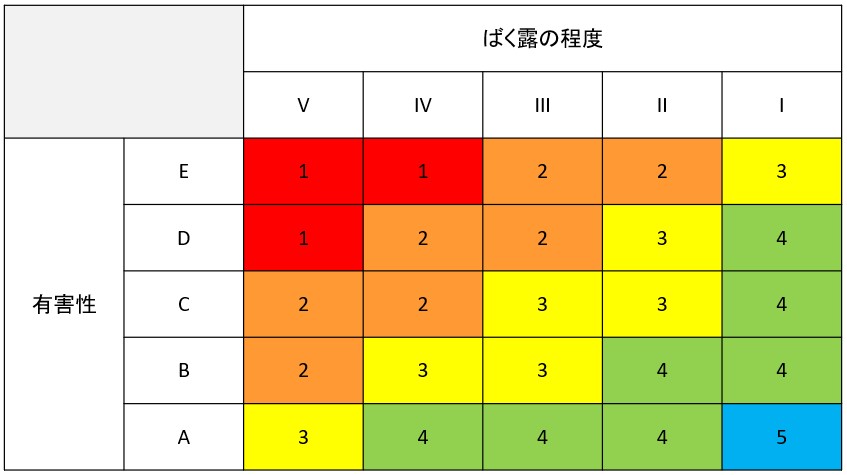
まずは縦軸:有害性の判断となりますが、これは簡単です。国際労働機関(ILO)が有害性の判断基準を作成していますので、これをAからEに落とし込めば完成です。
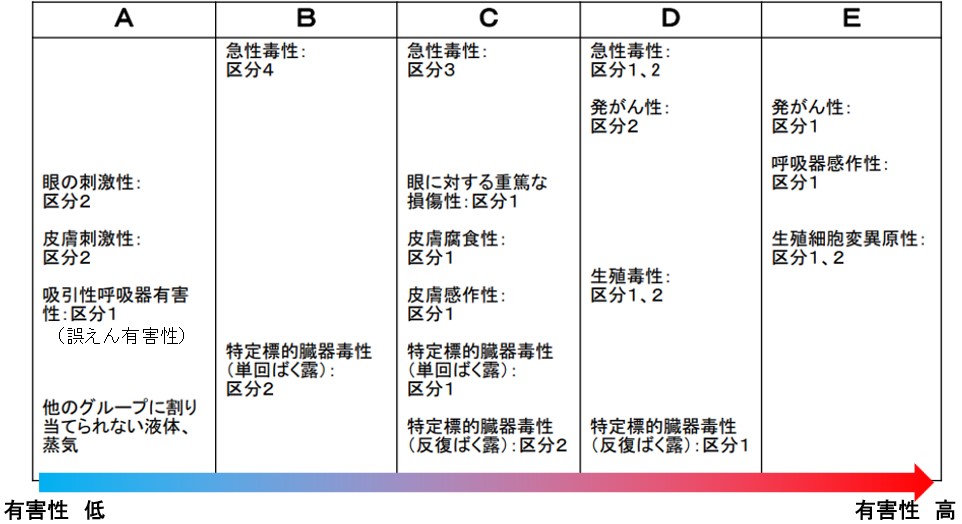
有害性の判断ができれば、あとはばく露の程度の判断ができれば、リスクを見積もることが可能です。こちらは少し面倒になっています。取扱量、揮発性・発散性、使用時の衣服汚染の有無、換気の状況を調べる必要があります。作業によって変わってくることなので、一回やれば終わりということではなく、作業ごとにリスクアセスメントをするのがいいでしょう。
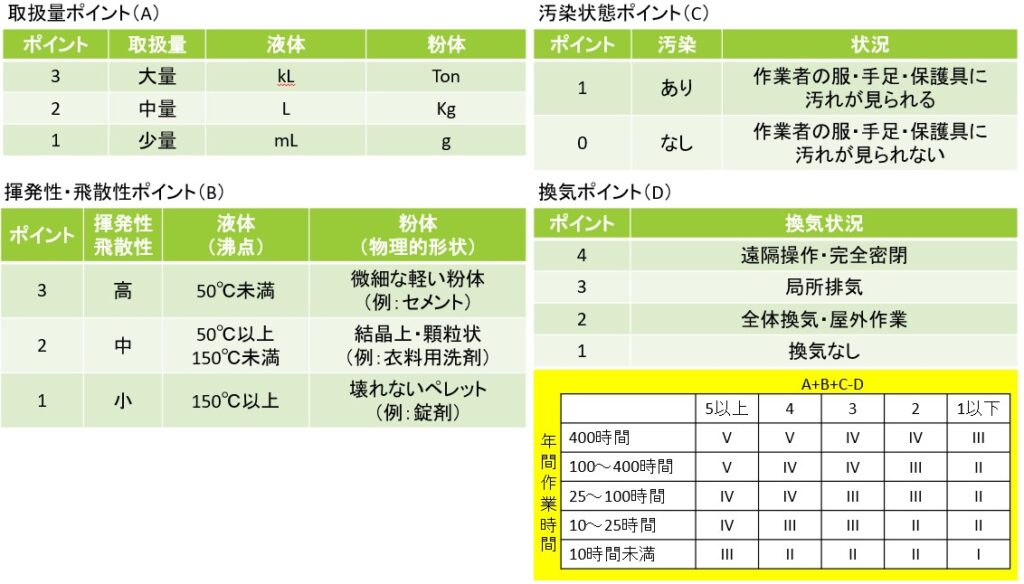
次に数理モデルになります。 MORE COMING SOON